

In pneumatic conveying, engineers generally refer only the velocity of the air (rather than the velocity of particles being conveyed), since this quantity can readily be calculated or measured. The margin, however, must not be too great because pressure drop, and hence energy required, varies approximately with the square of the velocity. A safety margin of about 20% on conveying air velocity is generally recommended. In this case, the minimum conveying air velocity may be as low as 5 m/s (~1,000 ft/min). For materials with good air-retention characteristics or good permeability, however, dense-phase conveying may be possible. For materials conveyed in dilute phase (suspension flow) this velocity is likely to be in the range of 15 m/s (~3,000 ft/min), and for many materials, dilute-phase conveying is the only option with a conventional pneumatic conveying system. In pneumatic conveying, however, the objective is to have the conveying air velocity maintained at a minimum value that is still sufficient to reliably convey the material. Therefore, the air velocity must be kept to as low a value as possible to avoid excessive pressure drop. From basic fluid mechanics, pressure drop is directly proportional to the square of the velocity. These include pipe wear, particle degradation, dust formation and others.Ĭonveying air velocity is a critical parameter in pneumatic conveying. This article provides information about the behavior of pneumatically driven solid materials and the problems that can arise due to impact of the solids on pipe walls and other particles. The geometry of the bend is an additional variable here because the radius of the bend will have a major influence on the impact angle.

The situation with regard to bends, however, is very different because all the material will have to take the turn, and, as a consequence, there will be a considerable number of particles impacting with the bend wall, as well as particle-to-particle interactions in the turbulence generated. In this case, the particle impact is likely to be a glancing blow and hence at a low angle of impact. In horizontal sections of pipeline, there will be a natural tendency for the particles to fall to the bottom of the pipeline due to gravity. The impacts also lead to reductions in particle velocity. This will be particularly so at each bend in the pipeline, where the particles will be subject to a change in direction, regardless of pipeline orientation.
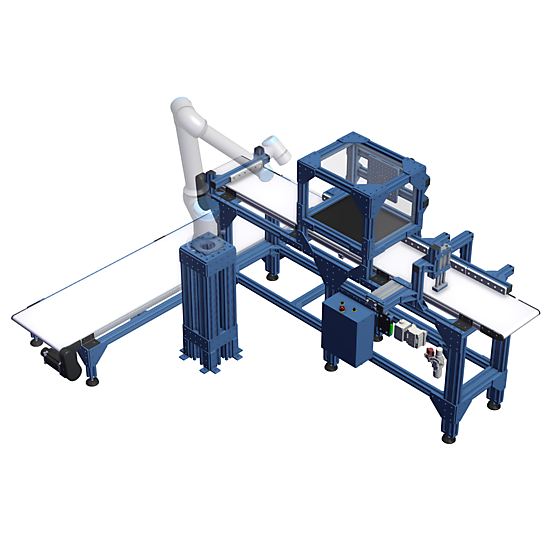
In traversing a pipeline, however, there will inevitably be impacts between the particles being conveyed and the retaining pipeline. By this means, any obstructions in the routing can be avoided simply by routing the pipeline around them. Powdered and granular materials can be conveyed vertically up and vertically down, as well as horizontally, in a single continuous routing, just by using bends in the pipeline. Provided here is an outline of potential problems related to particle impacts and the physics behind themĪmong the defining features of pneumatic conveying is the flexibility that can be achieved with pipeline routing for the transport of bulk particulate materials in a totally enclosed environment. Pneumatically conveyed solid materials inevitably impact pipe walls and other particles, which can create processing and equipment problems.
